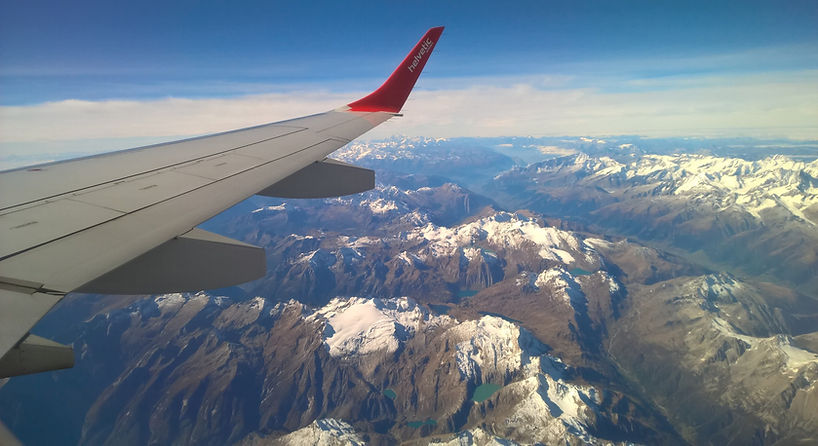
Analysis
The design that was conceived of by watching pizza ovens and follows similar design trends. Some of the design ideas that were discarded included using open flames or gas furnaces because the oven will need to run off of 240VAC. Detailed design choices like the element design, control casing design, and material selection for the control casing are detailed in the design matrices below. The analyses conducted are meant to define the requirements the heating system must meet in order to be approved for use in the overall oven design. These requirements are…
-
The heating system must heat up to 500° C
-
The heating system must be able to hold temperature for 30 minutes plus or minus 5° C
-
The heating system must be able to get up to temperature in 15 minutes
-
The heating system must fit within the housing design
-
The overall system must not exceed 250 pounds
-
The heating system must not be in direct contact with the carbon fiber.
01
System Power Consumption
The first analysis aimed to discover the total power consumption for the oven system. This was done to fulfill requirement 2, the oven must maintain temperature for the 30 minute heating cycle. First the radiant loss of temperature through the wall panels was calculated, then the energy required to raise the product and racks to temperature was analyzed. Finally, the exhaust loss was calculated, and the total energy use was calculated to be 34,509.2 BTU/hr.

02
Cartridge Bearing Thermal Expansion
The second analysis aimed to discover displacement of the heating cartridge bearing due to thermal displacement. This was done to satisfy requirement 4 where the heating system must fit within the oven environment. Using thermal displacement, the way the bearing will move during the heating process was calculated to be 0.089in horizontally, .0056 in longitudinally, and .00042 in vertically. This satisfied the design parameter of having the heating cartridges better secured and to make sure they will not shift whilst in the heating process.

03
Carbon Fiber Amount
Analysis 3 aimed to find the amount of carbon fiber that runs through the machine every hour. This helped with analysis 4 where the total wattage depends on the amount of substance being heated during the time allotted which satisfies requirements 1 and 3 . The total weight came out to be about 15.81 pounds using this information will help establish the design parameter of how much power the heating element needs to meet requirements 1 and 3.
04
Required Wattage
Analysis 4 was done to determine the necessary wattage to heat the carbon fiber in the correct amount of time to satisfy requirements 1 and 3. This determined how powerful the heating cartridges needed to be and how many heating cartridges were needed to meet the time requirement. Using analysis 3 the necessary value of 10.417 kilowatts of power was calculated to be needed. This establishes the design parameter of needing 6 heating cartridges since each has 2000 watts of power.


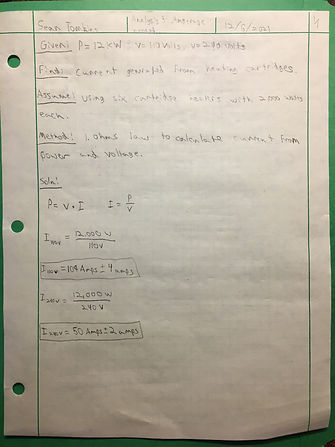
05
Amperage Ratings
Analysis 5 was done to establish the current values that would be generated from the 6 heating cartridges this satisfied requirements 1, 2, and 3. Since the current exceeds the allowable limit the entire system will not function. The current values were calculated for using a 110-volt source and a 240-volt source. The values then came out to be 109 Amps for the 110-volt source and 50 Amps for the 240-volt source. This established a design parameter of needing a 240-volt source to practically operate the heating cartridges.
06
Screw Stress
Analysis 6 was done to establish the overall stress the two screws that will secure the heating control system to the oven will experience satisfying requirement 2 by securing the controls necessary for regulating the heat to the oven. The analysis calculates how much force the screws experience while stationary which will be useful to ascertain how much more force, they can handle without being permanently deformed or broken which was calculated to be 7.819 pounds. This established the screw size design parameter.


07
Critical Stress For Cartridge Bearing
Analysis 7 was done to determine the critical stress for the cartridge bearing satisfying requirement 4 by calculating the critical stress for the bearing that will secure the heating cartridges in the oven environment. This will help to determine what kinds of stresses and loads the bearing can handle as well as determining whether it can secure the heating cartridges. It was determined that the critical load was 68.47 pounds with a allowable load of 34.2 pounds, and critical stress of 456 psi. This established a design parameter of the bearing being made of ASTM 1011 Hot Rolled steel.
08
Surface Area Loading
Analysis 8 was done to determine the surface area loading that is going through the heating cartridge being used for this project satisfying requirement 1. This value can be compared with suggested ranges to determine if the heating cartridges is at risk of damaging itself when heating up. The surface loading range needed to be greater than 8 and less than 12 watts per inch squared and the value was calculated to be 8.55 watts per inch squared which is within the proper range. This affirms the design parameter of using the 2000-watt heating cartridge.


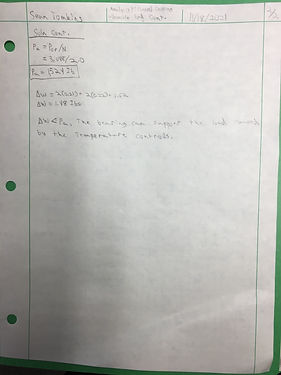
09
Control Casing Bearing Critical/Allowable Load
Analysis 9 was done to determine the critical and allowable load for the control casing bearing satisfying requirements 2 and 6. This helped to determine whether the bearing will be able to support the static load or if a new stronger material will need to be chosen to construct the bearings. The critical load came out to be 3,048 Ibs and the allowable load came out to be 1,524 Ibs. This affirms selecting a 6061-T6 aluminum sheet for the material.
10
Heating Cartridge Thermal Expansion
Analysis 10 was done to determine the heating cartridge displacement due to thermal expansion satisfying requirements 4 and 6. This helped describe the changes that the heating cartridge undergoes whilst conducting its heating cycle. Although the findings from the analysis confirm it will not move very much if it did prove to be too much then a new kind of heating element would need to be selected. The cartridge will undergo a 0.056-inch displacement along its length horizontally and its diameter will increase 0.0042 inches vertically.
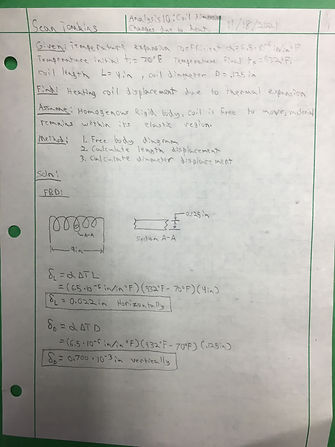

11
Heating Cartridge Internal Stress
Analysis 11 was done to determine the Internal Stress along the heating cartridge’s internal axis satisfying requirement 1. This will help prove whether the heating cartridges can undergo its heating cycle without causing any permanent damage to itself. By calculating the force acting on the cartridges internally the internal stress was determined to be 162.39 psi which will not cause any permanent damage to the heating cartridges.
12
Heating Cartridge Critical Stress
Analysis 12 was done to determine the critical load and stress for the heating cartridge to satisfy requirement 1. This will help determine whether the heating cartridges will yield and/or buckle due to stresses it may face. The analysis was done by calculating the slenderness ratio and C ratio to determine which critical load equation needed to be used. After determining that the Johnson formula was needed the critical load was calculated to be 15,334 Ibs giving a critical stress of 35,172 psi.
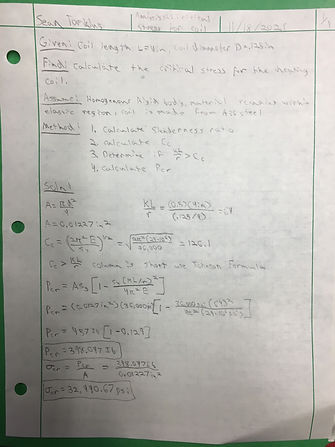